Embedded computers make inroads to vision applications
Embedded vision systems are replacing industrial PCs in machine vision and image processing applications
Whether running general purpose operating systems (GPOS) such as Windows or real-time operating systems (RTOS) such as VxWorks, PCs form the heart of many of today's machine vision systems. However, unlike PCs developed for the consumer market, the PCs used in industrial applications must be capable of withstanding shock and vibration in harsh environments, incorporate industrial networking standards, high-performance CPUs and commonly used camera-to-computer interfaces.
In the past, it was the task of the systems integrator to configure these PCs to meet the needs of their particular application using off-the-shelf motherboards, I/O controllers and frame grabbers. Now, however, a number of companies offer embedded PC systems specifically tailored for industrial and machine vision applications. By incorporating standard camera and industrial interfaces and I/O, these PCs alleviate the need for systems developers to configure such systems, allowing them to concentrate more on the vision problem needed to be solved.
Because of the increased use of machine vision in industrial applications, a number of traditional industrial controller manufacturers are now targeting the embedded vision market. Indeed, at last year's VISION 2014 trade show in Stuttgart, 11 companies exhibited such products (see "VISION 2014 spotlight: Industrial PCs for machine vision," http://bit.ly/1PVUcQK). While such controllers have traditionally used interfaces such as Gigabit Ethernet for communications, the increased use of such standards allows them to be targeted for machine vision applications. Indeed, as such embedded controllers emerge, the distinguishing features between them and traditional systems offered by established machine vision companies is slowly blurring.
Industrial control
Many of today's industrial controllers feature embedded i7 Intel processors, multiple I/O channels, display output capability and support for dual SATA raid systems. Often these are fanless, making them suitable for factory environments. While some offer the ability to add extra board-level peripherals, many simply offer Gigabit Ethernet or USB interfaces. For developers wishing to interface to higher-speed, deterministic interfaces such as Camera Link, industrial controller manufacturers and machine vision vendors now offer embedded systems to support such interfaces. Indeed, because of the blurring differences between many of the functions of industrial controllers and vision processors, the choice of which camera and camera interface can rapidly narrow the choice of which to use.
In some cases, an embedded industrial controller or machine vision system may not provide the correct type of interface required. In such cases, systems integrators can choose from a number of CPUs and add-in boards with which to develop an embedded system. Then, by using PMC, XMC, FMC mezzanine or PCI Express Mini frame grabber cards, numerous analog and digital interfaces can be accommodated (see "Frame grabbers add features and formats," Vision Systems Design, June 2015; http://bit.ly/1N07Sfp).
To accommodate other peripherals such as digital I/O, WiFi and communication protocols such as PROFIBUS, however, will require the use of multiple add-in cards, making the systems integration task more complex. Rather than take this approach, systems developers can choose from a number of industrial controllers that can be expanded to support such interfaces while already integrating much of the functionality required by industrial control systems. In the design of its fanless C6930 industrial PC series, for example, Beckhoff Automation (Verl, Germany; www.beckhoff.com) has incorporated an Intel i7 processor, SATA RAID controller, two Ethernet interfaces, hard disk and an open mini PCI slot that can be populated with Mini PCI fieldbus cards for PROFIBUS, CANopen and DeviceNet control.
Camera interfaces
While such industrial PCs are used in traditional factory automation applications, other manufacturers have taken this concept further offering products that offer the functionality of industrial controllers and the capability to support multiple camera interfaces. While many of these support computer-based interfaces such as USB 3 and Gigabit Ethernet, others feature PCI-based expansion slots that can be used to support numerous types of analog and digital interfaces.
Both Advantech (Milpitas, CA, USA; www.advantech.com) and ADLINK Technology Inc. (San Jose, CA, USA; www.adlinktech.com) offer controllers that support both Gigabit Ethernet and USB 3. Featuring an Intel Core i7 processor from Intel, Advantech's AIIS-1240 (PoE) controller uses an Intel i210 LAN controller to synchronize camera data from two or more cameras using the IEEE 1588 standard.
To support Power over Camera Link and Power over Ethernet (PoE), ADLINK offers two embedded controllers, the EOS-4000 and the EOS-1200. Both based on the Intel i7 processor, the EOS-4000 supports two independent Camera Link Base PoCL ports with and pixel clock rates to 85 MHz, trigger and encoder input and two independent RS-232 serial communication ports, 64 isolated digital I/O connectors and an internal USB ports (Figure 1). Four independent PoE Gigabit Ethernet ports are supported on the EOS-1200 and IEEE 1588 for synchronizing multiple cameras.
While both Advantech and ADLINK also offer expandable industrial controllers that can be also be tailored to meet the needs of industrial machine vision applications, so too do companies such as Neousys (Taipei City; Taiwan; www.neousys-tech.com) and Vecow (New Taipei City, Taiwan; www.vecow.com). In addition to its integrated four port PoE and four USB3 ports, Neousys' Nuvis-3304af vision system can be expanded using two Mini PCI-E sockets and one PCI and one PCI Express slots (Figure 2). Thus, the unit can be configured to interface to analog, IEEE 1394, Camera Link or CoaXPress cameras. To provide a deterministic timing correlation between input and output signals, the Nuvis-3304af vision system uses a standalone embedded microprocessor to allow developers to configure the output delay and duration of the systems multiple digital I/O channels.
Vecow also offers a range of fanless controllers that feature multiple I/O interfaces, PoE, USB 3.0, USB 2.0, IEEE 1394 and PCI, PCIe and Mini PCIe expansion slots. Powered by an Intel i7 processor, the company's ECS-7710 controller, for example, integrates 2 Gigabit Ethernet LAN, 4 Gigabit PoE ports, and one PCIe x16 expandable slot.
Vision systems
While such systems are expandable, established machine vision companies such Teledyne DALSA (Waterloo, ON, Canada; www.teledynedalsa.com), Datalogic (Bologna, Italy; www.datalogic.com), National Instruments (Austin, TX, USA; www.ni.com) and Matrox (Dorval, QC, Canada; www.matrox.com) have taken a different approach. Rather than offer expandable vision systems, the machine vision systems these companies offer support camera-to-computer-based interfaces in enclosed fanless systems.
While these may not be expandable to support multiple camera interfaces, they are often supported by the companies own software packages and cameras. In this way, systems developers can leverage both the power of vision processors and vision-specific applications and experience that each company offers.
Many of these products support Gigabit Ethernet and USB 3 Vision camera interface standards. Both Matrox and National Instruments offer products that support both Gigabit Ethernet and USB 3 Vision. Matrox's 4Sight GPm, for example, is a fanless design with four PoE GigE Vision and four USB 3 Vision ports. Real-time I/O management is achieved through a dedicated hardware that enables output events to occur at precise moments in time, based on elapsed time, or specific input events from discrete inputs such as rotary encoders. Shipped with Windows Embedded 7, the 4Sight GPm is supported by the company's MIL software package.
Like Matrox, National Instruments' Compact Vision Systems are also fanless units that support both USB3 Vision and GigE Vision cameras. Unlike Matrox, however, the company's Compact Vision Systems cannot be used to support both types of interface. Rather, the company offers two different controllers - the CVS-1459RT that features two USB3 Vision ports with dedicated bandwidth per port and the CVS-1457RT that features two PoE GigE Vision ports.
To support multiple camera interfaces such as GigE Vision, Base Camera Link and IEEE 1394, NI has, in the past, offered a number of real-time vision systems. However, according to NI, these are not recommended for new designs.
Datalogic also offers a series of vision processors that support PoE cameras. While the entry-level MX20 Series is based on an Intel T3100 dual-core 1.9GHz processor and has two independent PoE camera ports, the MX40 incorporates an Intel P8400 dual-core 2.26GHz processor and four independent PoE ports while the MX80 features four PoE ports, an Intel 2.1GHz i7 quad-core processor and 16 isolated digital inputs and sixteen isolated digital outputs (Figure 3).
This processor is also used in the GEVA-3000 family of vision processors from Teledyne DALSA. The GEVA-3000 family is available in two models, supporting either six Gigabit Ethernet cameras or dual Base or single Medium capture from Camera Link cameras. In the Gigabit Ethernet version, trigger and power to the cameras is provided by an external I/O module. This is used to interface the GEVA-3000 to the company's line of Gigabit Ethernet Genie cameras as well as provide I/O capability (Figure 4). When choosing which embedded vision controller to purchase for a particular application, developers must tradeoff cost, time-to market, flexibility and software support.
While building an embedded system using off-the-shelf CPU boards, frame grabber and I/O controllers may prove the least expensive, expandable-preconfigured systems may alleviate much of the systems integration tasks faced with integrating these components. Purchasing stand-alone systems from established vision vendors, while perhaps more expensive, may offer the developer the least headaches since any machine vision software offered by the vendor will have been tested in a number of different applications.
Companies mentioned
ADLINK Technology Inc.
San Jose, CA, USA
www.adlinktech.com
Advantech
Milpitas, CA, USA
www.advantech.com
Beckhoff Automation
Verl, Germany
www.beckhoff.com
Datalogic
Bologna, Italy
www.datalogic.com
Matrox
Dorval, QC, Canada
www.matrox.com
National Instruments
Austin, TX, USA
www.ni.com
Neousys
New Taipei City, Taiwan
www.neousys-tech.com
Teledyne DALSA
Waterloo, ON, Canada
www.teledynedalsa.com
Vecow
New Taipei City, Taiwan
www.vecow.com
About the Author
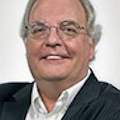
Andy Wilson
Founding Editor
Founding editor of Vision Systems Design. Industry authority and author of thousands of technical articles on image processing, machine vision, and computer science.
B.Sc., Warwick University
Tel: 603-891-9115
Fax: 603-891-9297