3D cameras measure packaged product volume
Logistics management companies plan, implement and control the efficient, flow and storage of goods, services and related information between the point of origin and the point of consumption. To ensure that such goods can be shipped cost-effectively, supply chain management companies such as Lebert (Kempten, Germany; www.lebert.com) must ensure that the weight and volume of such package is accurately determined so that the cost of transportation can be accurately billed.
In many countries, the price of transporting goods is determined by their weight. However, when large, lightweight packages must be transported, the volume of the products must also be used to determine the shipping price. While the weight of such products can be easily determined, their volume must often be determined manually.
To automate the task of such volumetric measurements, Lebert tasked Ametras Informatik AG (Baienfurt, Germany; www.ametras.com) to build an automated system to make it easier to track and trace both the weight and volume of such packages before they are shipped from warehouse (Figure 1).
"As packaged products enter the warehouse," says Jan Murray, Senior Software Developer with Ametras, "they are placed below three structured light-based cameras mounted onto a gantry." An operator then scans the packages barcode using a LS3578 wireless reader from Zebra Technologies (Lincolnshire, IL, USA; www.zebra.com). Data from this handheld scanner is then transmitted over a Bluetooth interface to the unit's cradle. Using a serial to Ethernet converter, data from the cradle is then transferred to a host computer where product and shipping data read from the barcode is stored.
As the barcode is read, the scanner also triggers the three structured light cameras. Each of the cameras then projects a synchronized dot pattern onto the package and the reflected, captured images are stored in each camera.
"Because of the large variety of packages that need to be scanned," says Murray, "three cameras were required to eliminate any effects of occlusion that would occur if only one or two cameras had been used." To reduce this effect, the center camera is positioned to take a vertical view of the package, while the other cameras are positioned off-axis. To further increase accuracy, multiple images are taken by each camera, averaged and filtered using the cameras built-in ARM-based PC.
Filtered images are then transferred to a PC where feature descriptors are computed that correspond to the reflected dots in the three images, and a point cloud generated using OpenCV and Point Cloud Library (opencv.org). From this point cloud, the volume of the package is then calculated.
Of course," says Murray, "the accuracy of the system will depend on the kind of materials scanned by the 3D cameras. For most materials, the system is accurate to within 5%. However, if a product is wrapped in silver foil or highly reflective wrap, the system is accurate to within 10%."
At present, the system is in operation at Lebert a nd according to Dominik Herr, Freight Forwarding Manager, will most likely be deployed in several of the company's facilities. Other companies, notably Raben (Heilbronn, Germany; http://deutschland.raben-group.com) and Gebrüder Weiss (Lauterach, Austria; www.gw-world.com), have also installed systems for evaluation.
About the Author
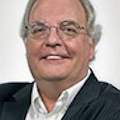
Andy Wilson
Founding Editor
Founding editor of Vision Systems Design. Industry authority and author of thousands of technical articles on image processing, machine vision, and computer science.
B.Sc., Warwick University
Tel: 603-891-9115
Fax: 603-891-9297