Vision guided robotics system wins Smart Vision Lights application contest
ControlVision’s Clara Dunning, a marketing manager, has won the 2013 Smart Vision Lights application contest for a robotic system designed for the automation and inspection of plastic production.
When plastics company Sistema introduced a new range of plastic food containers that used smaller clips, issues in the manual production process led to the search for an automated solution. In order to keep with up demand, Sistema tasked ControlVision with the integration of an automated system that would ensure accuracy for the clip placement while maintaining speed on the conveyor belt, according to the Smart Vision Lights press release.
Dunning’s systems utilizes two BaslerScout scA640-74gm cameras that capture images of the clips as they are carried on dual conveyor belts. The cameras feature ½” Sony ICX414 CCD image sensors and 650 x 494 pixels with 9.9 µm x 9.9 µm pixel size. In addition, the cameras feature GigE interface, external triggering, and programming exposure control via the camera API. Encoder feedback is employed to enable the accurate tracking and moving and two Smart Vision Lights DLP-300x300-WHI lights provide lighting in the inspection system. After the images are captured, they are sent to the VisionServersoftware to determine position.
Once the software determines the position of the plastic clips, VisionServer then commands one of the Dual Adept Cobra s600 robots to pick up the clip. A separate camera then captures an image of a corresponding plastic lid, which is also processed by VisionServer to locate position. The robot then applies the clip onto the lid and the process is repeated for the second clip (and so on.) ControlVision’s VisionServer framework acts as the human-machine interface, monitoring the entire process.
As a result of the implementation of the system, clips are now applied to lids at a rate of one every two seconds, which is double the output of the previous system, according to the press release.
View the Smart Vision Lights press release.
View more information on ControlVision.
View more information on Basler.
Also check out:
Robotic factory automation system reduces costs, increases productivity
Vision automates jar inspection
Inspection system boxes clever
Share your vision-related news by contacting James Carroll, Senior Web Editor, Vision Systems Design
To receive news like this in your inbox, click here.
About the Author
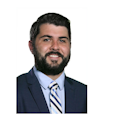
James Carroll
Former VSD Editor James Carroll joined the team 2013. Carroll covered machine vision and imaging from numerous angles, including application stories, industry news, market updates, and new products. In addition to writing and editing articles, Carroll managed the Innovators Awards program and webcasts.