MIPI A-PHY: An Interface for Industrial Embedded Vision
What you'll learn:
- How A-PHY (a physical layer protocol developed by the MIPI Alliance) can be used in industrial applications, such as automated inspection or robotic pick-and-place.
- Characteristics of A-PHY, such as its long reach and low power consumption, that lend themselves to machine vision systems used in industiral automation.
Machine vision has been in use for decades on the factory floor for automated quality inspection and process monitoring. Industrial vision systems have traditionally been operating on PCs because of the high processing power required to analyze large image data. However, the latest developments in processor technology and AI open new opportunities to implement industrial vision on embedded systems, reducing form factor and cost.
A-PHY, an embedded vision interface standard originally designed for automotive applications, has benefits for industrial vision systems in terms of bandwidth, cable length, EMI performance and scalability.
What is MIPI A-PHY?
A-PHY stands for Automotive PHYsical layer. It is a high-speed, long-reach physical layer protocol developed by the MIPI Alliance (Bridgewater, NJ, USA). Originally developed for automotive applications, it is designed to enable high-speed data transfer over long distances while maintaining low power consumption, which helps ensure that machine vision systems can function seamlessly even in harsh industrial settings. These features make it attractive for vision systems in industrial environments for such applications as in-line quality inspection and warehouse automation.
Related: Delivering High-Resolution Machine Vision for Enterprise Drone Applications
Here are the characteristics of the MIPI A-PHY that enable the interface to perform well in embedded vision applications.
1. High-Speed Data Transmission
Most industrial machine vision applications are time-critical: High-resolution images must be transmitted and processed in real-time to detect defects and sort out non-conforming products without slowing down the production line. This requires high-bandwidth camera interfaces.
MIPI A-PHY is engineered to operate safety-critical vehicle equipment such as autonomous driving or driver assistance systems. It provides high-speed data rates (up to 32 Gbps) over long distances, helping to ensure that the large amounts of data generated by machine vision cameras can be transmitted quickly and reliably without compromising image quality.
2. Long Reach
Industrial inspection systems are often integrated in machines or robots and require sensors and cameras to be placed away from the processing unit—for example, to capture images of a product from different viewing angles. This is why an interface like Gigabit Ethernet is so popular in the industry, as it allows up to 100 m cable length. The MIPI CSI-2 standard of most embedded cameras and sensors, however, offers a very limited reach of a few tens of centimeters.
Related: MIPI Alliance Releases A-PHY SerDes Interface for Automotive
Implementing vision systems on a vehicle also requires longer cable lengths to connect cameras and sensors located outside the vehicle to a processing unit located inside and complex cable path to bypass mechanical parts or the passenger cabin. Therefore, A-PHY can support data transmission over distances up to 15 m or more, which is a crucial factor for applications where the camera or sensor may be far from the processing unit such as on a robot arm.
This extended reach provides engineers with flexibility in designing embedded vision systems, as devices can be placed further apart without sacrificing data integrity or performance.
3. Robust Transmission in Harsh Conditions
Industrial environments present unique challenges, including electromagnetic interference (EMI), vibrations, and harsh environmental conditions, and yet require a reliable image data transmission for quality inspection.
Because it has been designed for safety-relevant automotive applications, MIPI A-PHY provides noise immunity, and electromagnetic compatibility (EMC), making it suited for these challenging environments.
Related: How GigE Vision 3.0 Fits in the Machine Vision Ecosystem
4. Low Power Consumption
As an automotive interface, MIPI A-PHY is designed to operate off grid in an environment packed with many systems within a compact space. It has therefore been designed with low power consumption in mind. The interface’s efficient data transmission mechanisms help ensure that machine vision systems can maintain high performance while minimizing the amount of energy used.
While power consumption is usually not as much of an issue in industrial machine vision as in mobile applications, it can be in specific use cases. Examples include situations in which component heating can significantly impact image sensor performance and reliability or can cause damage to neighboring systems or in mobile applications such as AGVs (Automatic Guided Vehicles) or AMRs (Autonomous Mobile Robots) in warehouse automation.
5. Scalability for Complex Systems
As industrial machine vision systems become more advanced, the need for a scalable architecture that can support a growing number of cameras, sensors, and other devices is more important than ever. MIPI A-PHY supports multiple cameras and sensors connected to a single data bus, providing a flexible, scalable solution that can grow with the system.
Related: AI and Rugged Edge Computing Are Fueling a Range of Applications
This scalability allows manufacturers and industrial operators to integrate additional sensors and cameras into their vision systems as the need arises, without overhauling the entire infrastructure. The ability to expand systems with minimal additional cost and effort helps ensure that companies can future-proof their machine vision systems.
6. Improved System Integration
Industrial machine vision relies on standards for reliable operation and interoperability between vendors of components such as cameras and image processing software.
MIPI A-PHY is compatible with MIPI CSI-2 (Camera Serial Interface) and other MIPI protocols to allow integration with existing embedded vision systems. This compatibility reduces the time and cost of integrating new components and technologies, helping manufacturers bring new products and innovations to market quickly.
Moreover, the availability of standardized interfaces with MIPI A-PHY ensures that the components in a machine vision system—such as cameras, sensors, processors, and displays—work together, improving overall system reliability and performance.
7. Reliability and Durability
Industrial environments often subject machines to harsh conditions, including extreme temperatures, vibrations, and electromagnetic interference. MIPI A-PHY has been specifically designed to perform reliably in such environments. The robust physical layer of MIPI A-PHY ensures data integrity even in the most challenging conditions.
Related: How Machine Vision Will Help Industry 5.0 Prioritize Humans
This durability reduces the need for frequent maintenance or replacement of system components, leading to cost savings over the long term and more consistent operational performance.
8. Future-Proof Technology
Because industrial machine vision is not a high-volume business, it has always used and adapted widespread standards from the IT or consumer electronics industries such as USB or GigE to benefit from their technology advancements and economies of scale. Embedded vision is still in an early stage of adoption in machine vision. Therefore, it is only natural that system integrators want to choose a technology that is future-proof.
As an automotive standard, MIPI A-PHY is designed to be high-volume and future-proof, offering high-speed, long-range, and low-power capabilities that are likely to remain relevant as new technologies, such as AI-based vision systems and 5G connectivity, gain traction.
Related: What's New in CLHS Version 1.2?
The adoption of MIPI A-PHY also positions companies to benefit from the broader MIPI ecosystem, which is continuously evolving to meet the needs of industries like automotive, consumer electronics, and, of course, industrial automation.
By adopting MIPI A-PHY now, manufacturers can ensure that their vision systems are ready to incorporate the latest innovations without significant reengineering.
9. Affordable Cost
Building on A-PHY as a high-volume automotive standard offers cost advantages—not only through the use of low-cost, widely available cables and connectors but also in the hardware required for implementation.
While machine vision cameras based on CXP, GigE, or USB Vision typically rely on expensive FPGAs, A-PHY was designed for high-volume markets like automotive and leverages cost-effective application-specific integrated circuits (ASICs) instead. Replacing or eliminating FPGAs not only reduces hardware costs but also simplifies system integration—ultimately lowering development costs as well.
Related: GenICam: In the Engine Room of Machine Vision
MIPI A-PHY is not just a solution for automotive applications; it’s also suitable for industrial machine vision systems. Its high-speed data transmission, low power consumption, long reach, and durability make it a good choice for industrial environments that need high performance and reliability.
About the Author
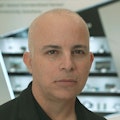
Moti Shtrobach
Moti Shtrobach is the vice president of business development at Valens Semiconductor (Hod Hasharon, Israel). He holds a Bachelor of Science (BSc) degree and brings over 25 years of experience in semiconductor development, including processor design for networking and connectivity applications. At Valens, Shtrobach leads business development efforts in the industrial, embedded, and machine vision markets, focusing on building strategic partnerships and driving adoption of high-performance connectivity solutions such as A-PHY.