Coty Cosmetics (London, England; www.coty.com), the manufacturer behind the Sally Hansen (New York, NY, USA; www.sallyhansen.com), Rimmel (London, England; www.rimmellondon.com), and CoverGirl (Cockeysville, MD, USA; www.covergirl.com) brands has in its Maryland factory 12 powder presses turning out a steady stream of powdered cosmetics products into metal pans called godets.
Each filled godet requires the proper volume of content, a smooth surface, and no errant material on the edge of the pan.
In the past, these inspection and measurement tasks were visual-only and subject to operator opinion. Samples were taken at startup to ensure proper fill levels. Then, at 15- to 30-minute intervals, samples were taken and tested. Chris Sydorko, owner of Sydorko Automation (York, PA, USA; www.sydorkoautomation.com), developed a 3D imaging system that replaced the manual inspection operation.
“The introduction of the vision system presented the customer with the knowledge that most of the product didn’t meet the existing specifications,” says Sydorko. “This drove a re-evaluation and ultimately a modification to the standard to adapt from a visual inspection to a digital inspection.”
Related: Machine vision battery tray inspection systems uses 3D scanning
The vision system is based on a DS1101 3D laser profiler from Cognex (Natick, MA, USA; www.cognex.com) (Figure 1). Sydorko specifically chose this model because it fit the needed field of view requirements. The profiler conducts three operations for inspection purposes: volume measurement to ensure proper fill, finite height detection to ensure the surface has no air pockets or powder on the lip of the pans above the nominal measured surface, and finite negative height detection to ensure the surface doesn’t have any holes, voids, or cracking below the nominal measured surface.
The profiler may conduct inspection operations on 10 different recipes. Operators change recipes using a human machine interface (HMI), on a display panel from Hope Industrial Monitors (Roswell, GA, USA; www.hopeindustrial.com) that’s connected to the CompactLogix controller via FactoryTalk Machine Edition software from Rockwell Automation (Milwaukee, WI, USA; www.rockwellautomation.com).The profiler conducts the godet inspection and sends the result information via Ethernet IP to an Allen Bradley L24 CompactLogix controller from Rockwell Automation . This information includes a scene number, pass/fail result, and pick location on the belt. Godets that fail inspection are placed into a rejection bin by a Universal Robots (Odense, Denmark; www.universal-robots.com) UR3-model robot arm.
The UR3 robot, a UR5-model robot, and the laser profiler are incorporated into a custom-designed mobile cart created by Sydorko using components from Robotunits (Cranbury, NJ, USA; www.robotunits.com). After being filled at the powder press, godets are placed onto the cart’s conveyor and a photo eye mounted over the conveyor triggers the laser profiler.
The photoeye also triggers an input within the robot controller to begin tracking the signal produced by a Banner Engineering (Minneapolis, MN, USA; (www.bannerengineering.com) push/pull incremental encoder, to track the positions of the godets.
The UR3 cobot picks up godets that pass inspection in groups of two or four, depending on the product, and places them onto a tray (Figure 2). Once the UR3 fills a tray with godets the UR5 robot picks up the tray, places it into a case, picks up an empty tray, and places the tray into the staging area for filling by the UR3 cobot. Trays and cases are stored on the cart, with fresh trays and cases loaded in by employees, as needed.
Sydorko constructed four of these lightweight, easy-to-move carts mobile carts. Two of the carts, stationed at high-volume presses, rarely move. The other two carts move every day, usually once every three shifts. Operators only require 15 to 30 minutes to prepare a cart to receive godets from the press.
Coty Cosmetics expects to save $500,000 annually from increased efficiency, thanks to the robot carts running three shifts, five days a week.
About the Author
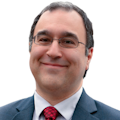
Dennis Scimeca
Dennis Scimeca is a veteran technology journalist with expertise in interactive entertainment and virtual reality. At Vision Systems Design, Dennis covered machine vision and image processing with an eye toward leading-edge technologies and practical applications for making a better world. Currently, he is the senior editor for technology at IndustryWeek, a partner publication to Vision Systems Design.