Standalone vision system targets small parts inspection
Machine vision solution provider and systems integrator Artemis Vision has developed the visionStation standalone vision system, which is designed to perform the inspection of small parts.
When it comes to small parts inspection, there are number of challenges that must be overcome, starting with space constraints. Some small parts manufacturers have limited space for inspection equipment, so it is important to understand the manufacturer’s needs and space requirements. Accuracy and repeatability must also be considered. Inspecting small parts by eyesight alone can be a daunting task, and maintaining a consistent method or process of inspection can change from person to person. Small parts inspection applications must be consistent for them to be successfully accurate and repeatable.
Lastly, for small parts inspection to be successful, the manufacturer needs to know what defects they are looking for, as some defects can be so small that they go unnoticed. Additionally, manufacturers need to catalog known defects, which becomes easy when machine vision is used, as opposed to human inspection.
Artemis Vision’s visionStation is precision machined from aluminum and fitted with a digital machine vision camera and lighting that is tailored to suit the type of inspection performed. The system is an operated-loaded unit that can be used as a standalone inspection station, or integrated into an existing operation.
"The visionStation is ideal for customers who need to run approximately 20,000 parts per day or less," stated Tom Brennan, President at Artemis Vision. "At 3 seconds per cycle, an operator can load about 10,000 parts per shift. Customers who need flexible automation and repeatability between operators and production batches without necessarily wanting or needing full inline automation where parts are conveyed on a belt."
Within the visionStation is a Prosilica GT4905 machine vision camera from Allied Vision. This camera features the KAI-16050 CCD image sensor from ON Semiconductor, which is a 16 MPixel sensor that achieves a frame rate of 7.5 fps through GigE interface. This camera was selected, according to Brennan, as a result of its "high resolution and excellent dynamic range."
"The dynamic range plays an important part when imaging the shiny areas of a part, created by the lighting source. Furthermore, the Prosilica GT4905 can handle the rigorous conditions the visionStation may be used in."
Software for the system includes utilizes Microscan’s Visionscape and Artermis Vision’s proprietary visionWrangler() software. "Our software is built from our extensive library of components – reading a data matrix, doing measurements, absence-presence and counts," explained Brennan.
The visionStation is offered in two sizes, the small and larger system measuring 1 and 1.5 cubic ft, respectively. The small system can accommodate parts up to 2 in. (5.08 cm), while the large system can hold parts up to 6 in. (15.24 cm). The minimum defect size allowance for each system size is: 0.003 in. (76.2 µm) for the small station and 0.01 inches (254 µm) for the larger station.
Artemis Vision builds visionStation systems based on the parts a manufacturer supplies and intends to have inspected. In the next generation visionStation, Artemis Vision reportedly plans to upgrade its sensor.
"We will likely upgrade to a newer CMOS camera and use C-mount optics," Brennan commented, "which will provide more lensing options and reduce the overall size of the unit."
View more information on Artemis Vision.
View more information on Allied Vision.
Share your vision-related news by contacting James Carroll, Senior Web Editor, Vision Systems Design
To receive news like this in your inbox, click here.
Join our LinkedIn group | Like us on Facebook | Follow us on Twitter
About the Author
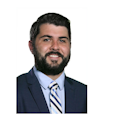
James Carroll
Former VSD Editor James Carroll joined the team 2013. Carroll covered machine vision and imaging from numerous angles, including application stories, industry news, market updates, and new products. In addition to writing and editing articles, Carroll managed the Innovators Awards program and webcasts.