3D welding helmet employs extreme dynamic range imaging
Welders must pause their work and flip up or remove protective visors to examine the quality of their welds, as the visor greatly reduces the welder’s visibility. A new image fusion process allows welders to finely examine their work in real time.
The arc welding process creates visible light so bright, and generates enough ultraviolet and infrared light, that welders must wear specialized helmets to prevent inflamed corneas and/or retina burns. The filter in the helmet’s lens shade darkens the scene to allow the welder to look directly at the weld site, which effectively blacks out the rest of the scene.
The Xtreme Dynamic Range (XDR) 3D weld visualization helmet, developed jointly by Kawada Technologies, Inc. (Tokyo, Japan; www.kawada.jp/global), Kawada Industries (Tokyo, Japan; global.kawada.jp), and research center SRI International (Menlo Park, CA, USA; www.sri.com), provides the required level of protection for welders without the wearer losing sight of the environment around the weld location and enhances the visibility of the weld tip and the welds themselves.
The helmet uses cameras from XIMEA (Münster, Germany; www.ximea.com) and The Imaging Source (Bremen, Germany; www.theimagingsource.com), which feature Sony (Tokyo, Japan; www.sony.com) CMOS sensors, and a low-resolution, radiometric longwave infrared imager from FLIR (Wilsonville, OR, USA; www.flir.com). Fine shutter synchronization enables the sensors to support microseconds-long exposure times, enabling the fast capture of multiple images with varying exposure settings. These images are fused together to create a 3D stereo vision stream with 150 dB dynamic range on a head-mounted display inside the helmet. With this dynamic range, operators can see weld beads during arc welding operations, which gives the welder a finer degree of control over the weld.
The display rate is fixed at 30 fps and image latency is under two to three frames, minimizing helmet operator disorientation through disconnect between physical action and visual display risks. An NVIDIA (Santa Clara, CA: www.nvidia.com) Jetson AGX Xavier 512-core GPU with an 8-core, Carmel ARM v8 64-bit CPU supporting 7.8 double-precision TFlops performs the image fusion.
The GPU is typically attached to the welder’s belt and tethered to the helmet, which features hot-swappable batteries for extended use.
This story was originally printed in the November/December 2019 issue of Vision Systems Design magazine.
About the Author
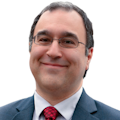
Dennis Scimeca
Dennis Scimeca is a veteran technology journalist with expertise in interactive entertainment and virtual reality. At Vision Systems Design, Dennis covered machine vision and image processing with an eye toward leading-edge technologies and practical applications for making a better world. Currently, he is the senior editor for technology at IndustryWeek, a partner publication to Vision Systems Design.