Robots and robotic-based vision systems are slowly replacing the tedious, time-consuming tasks involved in wine production.
While vision-guided robots are now common place in applications such as automotive inspection, materials handling and product packaging, they are now making inroads into more diverse fields such as agriculture. Here, the task of planting, fertilizing, picking and sorting produce has mainly been performed by manual laborers, who are faced with repetitive, laborious and time-consuming tasks. Indeed, according to Statista (New York, NY, USA; www.statista.com), in 2011, agriculture production in the United States required more than 750,000 people who generated a gross output of more than $374 billion.
Now, just as the manual tasks involved in the packaging and production of such foodstuffs has employed robots and robotically guided vision systems, machine vision technology is being employed in the more complex, less-constricted areas of farming.
Researchers at the Agriculture and Biological Engineering Group at the University of Illinois at Urbana-Champaign (Champaign, IL, USA; http://abe.illinois.edu), for example, see agricultural robotics as the logical proliferation of automation technology into agriculture, forestry and fisheries. However, just as it took a while for vision-guided robots to find widespread use on the factory floor, so too the proliferation of these agricultural robots will take time to be fully adopted.
Those at the University of Illinois see this occurring in three stages, first generation robots that are used as crop scouts to collect data such as crop stress and disease, second generation systems that perform field operations such as weeding, picking and pruning and third-generation fully autonomous systems that automate the complete process from seeding to packing.
Robots and wine
Today, a number of different types of robots are being deployed to tackle these tasks. In the wine industry, for example, numerous systems are now under development to perform the tasks of planting vines, pruning the vines, analyzing grape yield and type, picking, sorting and crushing grapes.
One of the most laborious of these tasks is planting the vines, traditionally a two-man process in which a manually-driven tractor is attached to a tree planting machine where another worker manually removes vines from a container and plants them in the ground as the tractor moves across the field. An example of this process can be found at: bit.ly/21mRwVI.
Needless to say, robotics researchers are looking to automate the planting process with the use of robotic systems. At the University of Victoria (Victoria, BC, Canada; www.uvic.ca), for example, Nick Birch and Tyler Rhodes, have developed a prototype system dubbed TreeRover, which carries up to 10 seedlings, and has a four-wheeled electric-drive base with an air-powered planting mechanism (Figure 1).
In operation, the robot drives to a planting site, punches a hole in the ground with a hollow metal tube and deposits a tree seedling using a compressed air mechanism. The surrounding earth is then secured around the plant. A video of the system in operation can be found at bit.ly/21x1nVH. By forming Iota Technologies (Victoria, BC, Canada; http://iotatechnologies.ca), they plan to upgrade the TreeRover prototype's planting mechanism, navigation system and powertrain and to allow it to carry more seedlings.
Are the grapes good?
Once planted, robots can be used to monitor factors such as grape yield, vegetative growth, and grape composition in the vineyard. This is the aim of an EU Project that has developed unmanned robot dubbed VineRobot (www.vinerobot.eu), that uses color cameras, IR thermography and GPS techniques to obtain agronomical and physiological data from the vineyard (Figure 2).
In addition to using a stereoscopic camera to aid navigation, the VineRobot incorporates a leaf sensor to detect nitrogen and a sensor that measures grape pigments to obtain information about the final wine color. By doing so, a complete map of the vineyard can be created that shows the quality of the crop in specific zones. A video of the VineRobot in operation can be found at: www.bit.ly/1oVU1xe.
To increase yield, prevent disease, and control excess growth, grape vines must be pruned every year. To hand prune a vine, the healthiest canes are selected and the rest are removed. For a robot to perform this task, the 3D structure of the plant must be computed, which canes to keep or remove determined and which cuts can be made without damaging other canes identified.
To perform this task, a research team at the University of Canterbury lead by Dr. Tom Botterill (Christchurch, New Zealand; www.canterbury.ac.nz) have developed a robotic system that is mounted on a platform that straddles the vines and moves along the row, pruning as it goes. The robot uses three cameras to image the vines, then computes a 3D model of the vine from these images. Software then determines which canes to keep and which to cut.
To do so, the system was trained to make good pruning decisions by providing it with examples of how pruning experts prune vines. Then, to prune the vines, a six-jointed robot arm reaches among the canes and makes the required cuts with a spinning cutting tool.
Automated picking
While planting, monitoring and pruning of vines can be performed by robotic systems, the task of picking the ripened fruit can also been automated. Unfortunately, the mechanical grape harvesters that are used for this task are rather primitive, simply vibrating the vines and transporting the grapes as they fall from the vine onto a conveyor to storage bins. A typical mechanical grape harvester in operation can be found at: www.bit.ly/1TkRBF2.
In doing so, the machine cannot rival hand picking where only the finest grapes are picked from the vine. However, to sort the grapes harvested by mechanical methods, Dr. Kai-Uwe Vieth of the Fraunhofer Institute for Optronics (Karlsruhe, Germany; www.fraunhofer.de) and his colleagues have developed a machine vision system to automate the process.
After the grapes are passed through a de-stemmer from Armbruster Kelterei-Technologie (Güglingen, Germany; www.rotovib.eu), the grapes are transported to a conveyor belt and into the system's sorting module. At the heart of the module is a line-scan camera that records the material flow imaging the fruit at 18,000 times a second. Software evaluates each image in milliseconds and controls air ejection units that blow foreign objects such as insects, vine shoots, stones or twigs out of the material flow. Not only does the system remove foreign objects, it also sorts the berries into various quality grades based on analyzing their shape and color.
Once sorted, the grapes must then be crushed, a task traditional performed by manually treading the grapes in large stone troughs known as lagares. This ruptures the cell walls of the grape skins without crushing the seeds. Today, many vineyards use robotic largeres that mimic the action of the human foot while eliminating the manual labor and cost once associated with this task.
Bottling and packing
After the wine is then poured into barrels and fermented, it is then shipped to be bottled and packed. Here again, this process has been automated. In a system developed for Concannon Vinevards, for example, ColloPack Solutions (Napa, CA, USA; www.collopack) has developed an automated production line to perform this task. In operation, a forklift operators transfers cases of empty wine bottles to a carton-depaletizing area where they are placed onto a conveyor. These cases are then transferred to a Model 94 decaser from A-B-C Packaging Machine Corporation (Tarpon Springs, FL, USA; www.abcpackaging.com) that automatically removes the bottles from the cartons, singulates them onto a separate conveyor and into systems that clean, then fill, cork and cap the wine bottles.
To inspect whether the correct fill level has been achieved, whether the cork is present and situated correctly in the neck of the bottle and whether the cap is present, the bottles are inspected by a CI Vision system from Mettler Toledo (Columbus, OH, USA; http://us.mt.com). If any bottles are found to be defective, they are then removed by a soft rejection system. Those that pass inspection are then capped and labeled and again inspected by the vision system. Finished bottles are then packed into cases and stacked onto palettes and shipped to the customer. A video of production line in operation can be found at bit.ly/1TYAsj9.
Customer satisfaction
When wine bottles arrive at a restaurant, the bottles are placed horizontally in wine racks. After a customer orders a bottle, the wait staff must then manually retrieve the bottle often from hundreds of similar wines.
To simplify this task, Bastian Solutions (Indianapolis, IN, USA; www.bastiansolutions.com) has developed a system that uses a small robot mounted on an AS/RS crane. The robot tooling uses an expanding bladder that fits around the bottle top in two locations and then places the bottle into a pick-up stand for a bartender. A video of the system in operation can be found at www.bit.ly/1QXNNsX.
Even after the bottle is opened, no sommelier or wine steward may be required to assess its quality. Professor Manel del Valle and his colleagues at the Universitat Autònoma de Barcelona (UAB; Barcelona, Spain; www.uab.cat), for example, have developed an "electronic tongue" that can identify different types of cava wines, automatically producing classifications similar to those of a sommelier and can be useful in detecting defects during the testing of these wines.
Currently, the electronic tongue currently can identify three types of cava: Brut, Brut Nature and Medium-Dry. However, with further training, it will identify all types available on the market. A description of the design of the system can be found at www.bit.ly/1RMFIEx.
While the use of fully automated vision-guided robotics in the production of food may present more complex problems for developers than factory automation systems, there is no doubt that the opportunities it allows developers of OEM products of vision components will be just as great.
Companies mentioned
A-B-C Packaging Machine Corp
Tarpon Springs, FL, USA
www.abcpackaging.com
Armbruster Kelterei-Technologie
Güglingen, Germany
www.rotovib.eu
Bastian Solutions
Indianapolis, IN, USA
www.bastiansolutions.com
ColloPack Solutions
Napa, CA, USA
www.collopack.com
Fraunhofer Institute for Optronics
Karlsruhe, Germany
www.fraunhofer.de
Iota Technologies
Victoria, BC, Canada
http://iotatechnologies.ca
Mettler Toledo
Columbus, OH, USA
http://us.mt.com
Statista
New York, NY, USA
www.statista.com
Universitat Autònoma de Barcelona
Barcelona, Spain
www.uab.cat
University of Canterbury
Christchurch, New Zealand
www.canterbury.ac.nz
University of Illinois at Urbana-Champaign
Champaign, IL, USA
http://abe.illinois.edu
University of Victoria
Victoria, BC, Canada
www.uvic.ca
About the Author
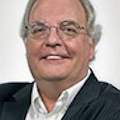
Andy Wilson
Founding Editor
Founding editor of Vision Systems Design. Industry authority and author of thousands of technical articles on image processing, machine vision, and computer science.
B.Sc., Warwick University
Tel: 603-891-9115
Fax: 603-891-9297