Edge Connectivity in Industrial Applications Using 10BASE-T1S Ethernet
Through automation, factories are becoming more intelligent and connected in ways we have not seen before. For these new systems to work effectively, reliable communication is essential, within industrial control panels themselves as well as to the devices that are distributed around the premises.
Until recently, industrial networks were complex and could require the use of a wide variety of protocols and gateways. This could be an expensive and unreliable way to ensure proper interconnectivity.
However, a transformation is underway with the advent of 10BASE-T1S Ethernet. This standard replaces legacy Fieldbus technologies, offering multiple benefits for modern networking environments and eliminating the need for gateways.
Supporting the new standard are a range of devices, such as transceivers, that provide a reliable and effective single-chip solution for interfacing to the twisted pair (TP) media.
Reliable Connectivity in Industrial Applications
While the distances are relatively short within industrial cabinets, providing reliable connectivity in industrial applications can be challenging, especially due to the significant amount of electrical noise present. Heavy switchgear, motors, and many other high current/high voltage devices can generate levels of electromagnetic interference (EMI) that corrupt network traffic.
Related: Targeting Automotive and Industrial Apps with 10BASE-T1S
In an office application, slow data transmission due to interruptions would be frustrating or inconvenient. However, in industrial applications, timely delivery of data is critical, especially from remote sensors that are controlling a machine. If data arrives late or incorrectly, process parameters may be violated or, worse still, the production machinery may be damaged.
For the same reason, it is important that data is transmitted in a timely manner. This excludes the use of some protocols where negotiation for access to the bus is based upon a random timeout.
How 10BASE-T1S Answers the Latest Industrial Connectivity Challenges
Network infrastructure is often conceptualized as a ‘stack’ with physical implementation (cabling/media) at the bottom and increasingly sophisticated software sitting above this. In Factory 4.0 applications, artificial intelligence (AI), machine learning (ML), planning, execution, automation (including inspection using machine vision), tracking, inventory control, supervisory control, etc. sit at the top. At the lowest (physical) layer is the factory floor where edge nodes—including robots, actuators, motion sensors, and valves—perform physical manufacturing work, often covering many assembly lines.
At the top of the stack, communication is via a multi-gigabit Ethernet LAN. However, factory floor communication tends to be a fragmented jumble of multidrop networking Fieldbus protocols including HART, RS-485, Mod-bus, DeviceNet, Profi-Bus, and CAN, running at megabits or less across a pair of twisted wires, which may be shielded or unshielded.
To allow this to work as a unified network, gateways are required between the Ethernet section and the other protocols, which fragments communication and adds cost and complexity.
A new form of Ethernet is set to enhance connectivity to the edge in factory applications such as automated inspection, machine tending, assembly, or sorting.
Related: Ubiquitous Ethernet and Its Many Protocols
The ratification (in 2019) of the IEEE 802.3cg specification delivered 10BASE-T1S. Based upon standard Ethernet, with a few important differences, this standard offers 10 Mbps throughput, multi-drop operation with deterministic collision handling. The standard runs on unshielded twisted single pair Ethernet (SPE) cables, thereby dramatically simplifying installation and reducing costs.
Deterministic operation is critical for real-time systems where it is important that messages are transmitted within a known amount of time. Traditional Ethernet uses CSMA/CD, which employs a random time period, and for this reason, there is no time guarantee on timely communications.
10BASE-T1S uses a new system known as PLCA (Physical Layer Collision Avoidance), which avoids data collisions on the bus. Under PLCA, a 2.0 µs beacon sent by Node 0 (coordinator) synchronizes the network nodes. Then Node 0 is given the opportunity to transmit. If there is no data, the opportunity is passed to Node 1 within the default standard 3.2 μs. This continues, giving each node a transmit opportunity in turn. Once the cycle is complete, a new cycle begins with a beacon signal from the coordinator. If a node attempts to transmit more than the permitted frame size, then a ’jabber’ function will interrupt and pass the transmission opportunity to the next node, thereby ensuring that the bus cannot be blocked.
Using PLCA, the worst-case media-access latency is calculated as the product of the number of nodes present and the maximum network frame size, which can be adjusted.
Many industrial applications are in harsh electromagnetic environments with radiated and conducted noise present due to switchgear, motors, and other heavy equipment. Despite the use of an unshielded twisted pair, 10BASE-T1S, offers excellent electromagnetic compatibility (EMC) performance compared to existing Ethernet protocols.
Related: New Technologies Extend the Life of Legacy Networks
In part, this is due to the deployment of PLCA. As the bus is known to be collision-free, the PHY receiver uses sophisticated algorithms to detect or recover the signal when high levels of noise exist in the environment.
Application and Deployment Scenarios
As well as its ability to operate deterministically, 10BASE-T1S is relatively low cost to deploy as it is based upon unshielded SPE cable. The cost savings and simpler integration of 10BASE-T1S can help to unlock a wide range of possibilities for applications that were previously hindered by budget or packaging restrictions. One such example is the ability to upgrade previously independent sensor nodes in complex industrial automation situations by connecting them to centralized networked systems. Previously available connection methods might have been either too expensive or hard to integrate, whereas 10BASE-T1S overcomes these barriers. Similar cost and packaging challenges can also occur during the design process of new robotic or automation solutions and once again, 10BASE-T1S can help to achieve greater interconnectivity without compromising performance or escalating budgets.
Related: Single-Pair Ethernet Comes Just in Time
In industrial applications, the performance and cost are of benefit, while noise immunity is particularly valuable. Here, 10BASE-T1S can be used to connect from the control cabinet to programmable logic controllers (PLCs), sensors, contactors, and any other device that is suitably equipped with a 10BASE-T1S interface.
(10BASE-T1S is not a perfect fit for machine vision due to the often very high data rates required for high-quality video streams. However, we believe it can be used for surveillance. We have demonstrated two vh.264 encoded video streams with 800 x 600 pixels and 25 fps running simultaneously on a 10BASE-T1S multidrop segment, utilizing approximately 65% of the available bandwidth, leaving some room for additional data. Therefore, it could be used for obstacle detection and avoidance in slow-moving machines.)
Conclusion
Until recently, networks in automated factories have been required to incorporate many gateways between edge devices and the main Ethernet network, due to the incompatibility of the protocols commonly used at the edge. Typically, there would have been several Fieldbus protocols including HART, RS-485, Mod-bus, DeviceNet, Profi-Bus, and CAN in operation, each requiring their own gateway. This added cost and complexity, not least as each gateway required software updates and maintenance.
With the advent of 10BASE-T1S, industrial networking has been simplified, and performance is enhanced at the same time. No longer are gateways required, and the edge connectivity has moved from sub-1Mbps Fieldbus protocols to 10 Mbps deterministic Ethernet.
About the Author
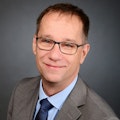
Arndt Schübel
Arndt Schübel is a product marketing engineer in the Analog & Mixed-Signal Group (AMG) at onsemi with 30 years of experience in digital design engineering and technical marketing.
He honed his skills in microcontroller design and ASIC applications. Since 2001, Arndt has served in various capacities at onsemi, such as digital ASIC design engineer, product marketing manager, and design center manager. Notably, Arndt also served as a system architect for Digital Mil/Aero ASIC during his tenure at onsemi, where he played a crucial role in shaping the architecture of complex systems. Currently, Schübel is a member of the technical staff at onsemi, where he continues to leverage his extensive knowledge and experience to provide technical marketing and applications support for SPE connectivity devices.