Rips, tears, skewed printing, and breaks during printing leads to financial losses for plastic packaging companies, making print quality inspection a crucial production step. When a midwestern company producing plastic packaging for food, consumer products, and medical and pharmaceutical companies wanted to upgrade from passive to automated inspection, it contacted One Box Vision (Clonmel, Tipperary, Ireland; www.oneboxvision.com) to develop a web inspection system capable of inspecting at speeds of 1000 ft./minute.
Previously, the company used a passive video camera system that enabled an operator to freeze an image, zoom in and out, and move around the image for print quality inspection. Not only does this method require human interaction, but it takes more time than a machine vision system would. To ensure and improve overall quality, One Box Vision built a complete print inspection kit called PackFlow based on off-the-shelf components and analysis software.
The system uses allPIXA pro line scan cameras and Corona II LED line scan lighting from from Chromasens (Konstanz, Germany; www.chromasens.de/en), along with Axion-CL 2xE Camera Link 2.0 frame grabbers from BitFlow (Woburn, MA, USA; www.bitflow.com) and an industrial PC from Vecow (New Taipei City, Taiwan; www.vecow.com). PackFlow also uses differential encoders from Encoder Products Company (Sagle, ID, USA; www.encoder.com).
To initiate the system, an operator acquires an image in register and either verifies it against its design file using a PDF verification system or verifies the image visually. Once the image is approved, all subsequent images match against that golden master image for verification. The software classifies any difference (defect) found in the web according to location, size, or intensity and stores up to 40 predefined quality thresholds for such classification.
Retrofitting the equipment into older printing presses presented the main vision challenge, as the presses caused plastic film stretching during printing, explains Conor O’Neill, General Manager, One Box Vision. To that end, the company developed the FlexRef algorithm, which runs in its ImageFlow machine vision software toolkit for web and sheet imaging.
“FlexRef deals with flexible packaging and allow for stretch compensation in plastic webs,” he says. “As printing occurs, the tension changes and plastic can be very thin, and it stretches during printing. The algorithm compensates for that stretch and allows for the proper alignment of images.”
A colored alarm light tower alerts an operator immediately when the software finds a defect. The system visually indicates the position and the nature of all detected defects on an HMI, allowing the operator to address the problem and correct the relevant effect, reducing inline waste. The software automatically records the relevant defect data in the database reporting tool, enabling easy tracking of the marked defects for later analysis and cleaning.
Potential cost savings comes in two forms. First, the system cuts down on inline waste, which can be quite a large percentage for a printer.
“Approximately 60% of revenue for one of these printing press operators is material costs, so the ability to reduce that by a few percentage points can make the difference between being profitable or not,” says O’Neill. “Sixteen months after installing the first systems for this company, the plant manager said the systems paid for themselves in under six months by way of reducing waste and customer claims.”
Secondly, compared to other systems, the system is based on an open design, so using commercial off-the-shelf technology instead of proprietary technology means that the total cost of ownership of the equipment over a certain period is cheaper than what incumbents can supply, suggests O’Neill.
“Take part replacement, for example,” he says. “This system does not lock someone down into any one manufacturer for components.”
Because of the success in the first installation, One Box Vision offers PackFlow as a complete print inspection kit in three options: a turnkey product, a kit, or as an OEM software license with application support. In the kit, the company supplies cameras, PC, and lighting along with its software. Turnkey systems involve the design and installation of an entire system based on individual requirements by One Box Vision.
Kits and full systems generally rely on the same standard set of components listed above. ImageFlow software is optimized for Intel CPUs but has also deployed with cameras from Teledyne DALSA (Waterloo, ON, Canada; www.teledynedalsa.com), and Basler (Ahrensburg, Germany; www.baslerweb.com).
About the Author
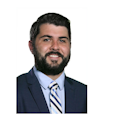
James Carroll
Former VSD Editor James Carroll joined the team 2013. Carroll covered machine vision and imaging from numerous angles, including application stories, industry news, market updates, and new products. In addition to writing and editing articles, Carroll managed the Innovators Awards program and webcasts.