Autonomous mobile robots streamline warehousing logistics operations
Logistics employees likely don’t want to spend an entire day driving a tractor or carrier around the warehouse picking up and dropping off pallets. Vision-guided robots offer a way to free a person up for more important tasks.
Wholesale work environment products company ICM (Odense, Denmark; www.icmsafety.com), for example, receives approximately 200 pallets of products per workday and 31,000 pallets each year that will ship out to customers at a later date. These products must be placed by forklifts in 12 m-high racks. Instead of paying someone full-time to perform this repetitive task, the company deploys three vision-guided robots from Mobile Industrial Robots (MiR; Odense; Denmark; www.mobile-industrial-robots.com).
Once in place, MiR1000 robots move palletized goods from a receiving area through narrow aisles, where the trucks place the items into racks, explains Søren Jepsen, Supply Chain Director. ICM employees place pallets on designated MiR racks from which the robots collect the pallets and transport them to certain aisles within the warehouse. Using an app, an operator sets up a mission on a tablet to dispatch the robots. The robots drop pallets at the end of the aisles, which high-reach trucks collect and place in relevant racks. Forklift operators communicate directly with the robots via an interface on the app and can always see truck locations on a map. Robots also make themselves noticeable by using audio signals and lights in busy areas.
Logistics and warehousing environments can be busy, cluttered areas. To navigate and avoid obstacles like racks, people, or other vehicles, the MiR1000 robots make use of 3D imaging and laser scanners. Two microSCAN 3 safety laser scanners from SICK (Waldkirch, Germany; www.sick.com) provide a 360° field of view at up to 30 m in a plane at 200 mm-height. To detect obstacles under or over the safety laser scanners field of view in front of the robot, the MiR1000 units use two RealSense D435 3D cameras from Intel (Santa Clara, CA, USA; www.intel.com), which feature a 120° horizontal field of view and detect objects 1700 mm-high at a distance of 950 mm in front of the robot.
Intel’s D435 USB 3.0 cameras make use of a 1920 x 1080 OV2740 CMOS image sensor from OmniVision Technologies (Santa Clara, CA, USA; www.ovt.com), and feature active infrared stereo depth technology, up to 1280 x 720 active stereo depth resolution at up to 90 fps, and a 1920 x 1080 RGB sensor capable of 30 fps. Additional sensors in the MiR robots include and accelerometer and gyroscope to sense inertial force, acceleration, and rotation; and encoders on each wheel to measure speed for accurate feedback to the laser scanners to detect the robot slipping on a wet floor, for example.
Equipped with the sensors and 3D cameras, the robots dynamically navigate using the most efficient routes while avoiding obstacles and automatically charge as required. The robots’ sensor systems also feed data into a planning algorithm, which lets the robot know where it drives and decides if the robot should adjust its path or make a safe and immediate stop to avoid collisions.
Additionally, the 53.1 in (L) x 36.2 in (W) x 12.6 in (H) MiR1000 robots weigh 509 lbs., have a payload of up to 2200 lbs. Each robot uses eight proximity sensors—two in each corner of an individual robot—to help the robot detect pallets and other low and otherwise hard-to-see obstacles. These prove necessary because the 3D cameras only provide data for the front of the robot, not on all four corners. Additionally, the proximity sensors point at the ground to detect objects below the field of view of the laser scanners on all four corners of the robot.
ICM’s setup consists of three mobile robots, four manned high-reach trucks, 10 manual stackers, and 26 dedicated employees. Overall, the mobiles save approximately 40 hours a week at ICM in the form of time spent on internal transport. Employees can now focus on higher-value activities like planning and optimization. Assessing, handling, and prioritizing pallets and the contents is complicated and requires insight and experience. Therefore, these tasks must be performed by human workers.
“Using the robots allows ICM to free up one employee for other, more value-creating tasks in the company,” says Jepsen. “MiR robots are here to stay at ICM, and perhaps even more will be needed.”
ICM management sees potential in automating more processes. Currently it is the flow from the good receiving area to storage aisles, but long term the company will automate transport from picking to the delivery of goods to get even more benefits from the robots.
Editor’s note: ICM purchased the MiR robots from the company’s Danish distributor, Baytech (Hejnsvig, Denmark; http://www.baytech.dk/)
About the Author
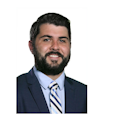
James Carroll
Former VSD Editor James Carroll joined the team 2013. Carroll covered machine vision and imaging from numerous angles, including application stories, industry news, market updates, and new products. In addition to writing and editing articles, Carroll managed the Innovators Awards program and webcasts.