Optical sensor increases spot welding efficiency for automated spot welding system
A joint project between fourresearch institutes and four industrial companies has resulted in the development of an automated system for the monitoring, optimization, and post-processing of electrode tips for resistance spot welding in the automotive industry.
The average car is held together by approximately 5,000 spot welds, but the more welding processes that are completed, the more the welding electrodes are worn out, which can lead to the spot welds becoming larger and the melting area between the plates becoming irregular to the extent that they no longer bond. As a result, production lines can be shut down for time and material-intensive maintenance intervals. The Fraunhofer Institute for Photonic Microsystems IPMS, along with the other organizations and companies, developed a system to design a fully automated system that addresses this issue and helps to optimize the process.
At the heart of the system, which is called the SmartDress system, is anoptical sensor developed by the Fraunhofer Institute that records the condition of the welding electrode and thereby calculates the time and extent of cleaning or mechanical post-processing required. Michael Leuckfeld, project manager at Fraunhofer IPMS, explained the process in a press release:
“Our system monitors both welding electrodes simultaneously from various perspectives,” he said. “We use diffusemonochrome LED lighting generated by opal glass for this purpose. The light is sent to the electrode via a mirror arrangement and beam splitter and then back to the photo detector. Lighting and image recording thus use the same optical elements.”
A prototype of the SmartDress is based on a passivecamera system that is controlled via an external computer and USB interface. The first tests under live production are scheduled to take place in 2014, and the system itself will be showcased in public for the first time at the Smart Systems Integration trade fair in Vienna from March 26-27.
The SmartDress project is a European Commission-funded project under the Framework-7 program. The project team consists of Sinterleghe srl. a producer of electrode tip dressing equipment, Fisher-Smith a provider of specialized visual system solutions, Finaids a provider of high spec industrial abrasives and Swantec a provider of modelling software for welding processes. Technical developments are driven by three research organizations; TWI responsible for the technical performance of the resistance spot welding process, VTT responsible for providing an abrasive dressing solution, and Fraunhofer IPMS, which developed the optical sensor.
View more information on theSmartDress project.
Also check out:
(Slideshow) Robots and research: Eight examples of innovative imaging applications
Vision guided robot picks and places bobbins
Medical wells scrutinized by high-speed automated vision system
Share your vision-related news by contactingJames Carroll,Senior Web Editor, Vision Systems Design
To receive news like this in your inbox,click here.
Join ourLinkedIn group | Like us on Facebook | Follow us on Twitter| Check us out on Google +
About the Author
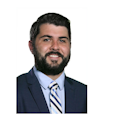
James Carroll
Former VSD Editor James Carroll joined the team 2013. Carroll covered machine vision and imaging from numerous angles, including application stories, industry news, market updates, and new products. In addition to writing and editing articles, Carroll managed the Innovators Awards program and webcasts.