Polarization 101: Concepts, techniques, and technologies
Polarization - Definition of Concepts, Techniques, and Technologies
Polarization, a filtering technique used for decades by photographers for image enhancement, also sees widespread use in commercial applications, including machine vision image acquisition. With polarizing cameras and imaging components increasingly entering the vision application mainstream since 2018, new applications and uses for polarization in machine vision continue to emerge.
Understanding the growing list of polarization applications requires a discussion of the latest polarization cameras and sensors and an understanding of the benefits and limitations associated with the use of polarization technology.
Polarization concepts
Light is a transverse wave, i.e. its electromagnetic and magnetic fields are disturbed at right angles relative to the direction of travel of the light waves. Or, it can be said that light waves oscillate perpendicular to their direction of travel.
Natural light, and virtually all artificial light (LEDs, incandescent lights, fluorescent lights, etc.) is unpolarized or weakly polarized. Natural light travels in any radial direction from the source of the light (Figure 1). Imagine a beam of light. Light waves oscillate 360° from every point along that beam. (An oversimplification, to illustrate the concept.)
Polarized light, on the other hand, is light in which the waves travel in only one, specific direction. Light can be polarized in nature by absorption, refraction, reflection, scattering, and birefringence (double refraction). For example, when light strikes water, it can be reflected linearly perpendicular, i.e. polarized in that specific direction, to the surface of water, which we experience as glare.
For another example, as the sun moves across the sky the angle of the sun’s light striking a window will change. At some point the light will reflect off the window, or be polarized, at an angle perceived as glare.
The sky is blue because sunlight strikes the molecular structure of the atmosphere and scatters, which polarizes the light in a specific direction. As the angle of the sun relative to the atmosphere changes the polarization angle of the light also changes, and the human eye perceives color changes from dawn to midday to dusk.
Polarization techniques
Returning to the example of the sun reflecting off the surface of water and producing glare, a photographer may employ a polarization filter to remove that glare, improving the image by filtering light at the specific angle causing the glare.
Similarly, in machine vision, artificial polarization techniques help developers select or restrict the direction of the light waves that enter a camera lens and strike an image sensor. The three basic ways to artificially polarize light are linear polarization, circular polarization, and elliptical polarization, with the latter two methods serving as extensions of linear polarization and not widely used in machine vision.
Dichroic, thin-film, and wire-grid polarizers represent the most common components used in machine vision to linearly polarize light. Wire-grid polarizers specifically can withstand the power levels of lasers, which can be useful in factory and scientific environments.
Polarization filters function by selecting or restricting light waves traveling in a single plane. The orientation of the filter determines the orientation of the light waves that can pass through the filter, thereby selecting one set of light waves to advance and preventing others from continuing (Figure 2).
Use of multiple filters, each of which prevent the passage of light waves at different orientations, allows finer attenuation of light. A filter only allowing vertical light to pass, followed by a filter only allowing horizontal light to pass, would act together to block most of the light waves passing through the filter pair.
Applications and implementation
Common polarization techniques in machine vision include inspection of glass and highly reflective materials. Raw and machined metal have grain at a microscopic level that can lead to linear polarization, making the use of a polarization filter useful. Plastic and glass, automotive, packaged materials, semiconductor, and LCD inspection applications commonly make use of polarization filters.
The proper way to employ polarization in an inspection environment typically involves polarizing both the light source and the reflected light (Figure 3) with a polarizer placed at the source of the light, at an angle that benefits the application, and a second polarizer placed at the same or a complementary angle, onto the lens of the camera conducting the inspection.
Even if the light projected onto an object is polarized in order to limit the potential number of reflective polarization angles, the reflective properties of the object may still create unwanted polarization when the light reflects off the object. Employing two filters allows for finer control of the light angles that enter the camera, ensuring the desired crispness of the image.
Placing a polarizer only over the camera lens, and thus only polarizing the light reflecting off the object to be inspected, may sometimes be an effective technique but far more often not. To demonstrate the point, consider the example of photography.
The polarizers used by photographers rotate, to allow the photographer to attune the polarizer to the precise angle at which the light is being polarized by the surface of the subject in the scene. The photographer tunes the angle of polarization as needed for different scenes, not a practical technique for automated imaging in machine vision.
Take, for example, parts on a conveyor belt rapidly passing underneath a camera for inspection. It’s impossible to achieve perfect, replicable results during parts inspection, even with polarized light and filter working in concert, because there will likely be variances in the position of objects relative to the camera, which affects the angles at which polarized light reflects off the surface of the object. However, a new technology and new components becoming readily available overcome the limitation.
New technologies and components
A polarizing image sensor makes a polarization filter part of the image sensor, versus a separate component placed over the sensor. The Photron Crysta by Photron (San Diego, CA, USA; www.photron.com) and PolarCam from 4D Technology (Tucson, AZ, USA; www.4dtechnology.com), to cite two examples, have been in the marketplace for some time and make use of on-sensor polarization.
The IMX250MZR/MYR (monochrome/color) Polarsens sensor from Sony (Tokyo, Japan; www.sony.com) represents a recent implementation of on-sensor polarization technology. The polarization elements are fabricated right into the silicon, under the microlens (Figure 4), which makes the sensor unique. In the color sensor, color filters are located directly underneath the polarizers.
The polarizers in Sony’s sensor, a microscopic implementation of a wire-grid polarizer over every lens on the sensor, have 0°, 45°, 90°, and 135° polarization angles in four-pixel groups. The groups are interpolated, reducing the sensor’s overall functional resolution by 4x. In other words, each four-pixel block equates to one pixel of output.
By interpolating the images from each four-pixel block, the sensor gathers considerable information about the linear polarization occurring on the surface of the object being viewed. These interpolated pixels allow a very accurate definition of the exact direction and intensity of the polarization within each four-pixel group.
DOLP, or degree of linear polarization (the intensity and direction of linear polarization as it’s interpreted from the four angles of each four-pixel group), and AOLP, or angle of linear polarization, (the angle of the light as it reaches the sensor plane) can be adjusted. Adjusting these parameters allows fine control of polarization similar to how a photographer rotates their polarization filter to achieve the desired crispness of image (Figure 5).
Software can then dynamically handle the selection of either individual wave angles, or the computational manipulation of the variety of wave angles, to analyze the image in ways that only were possible previously by providing sets of filters, multiple images, or even multiple sensors, to acquire multiple polarized analyses of the individual image, itself.
The dynamic process allows for the correction of glare that may originate from different angles on individual items to be inspected, making it easier to extract features, scratches, or even to see material stress in plastic.
Polarization techniques can also be deployed in line scan cameras like the quad-linear Piranha4 from Teledyne DALSA (Waterloo, ON, Canada; www.teledynedalsa.com), which has four linear sensor lines, each of which has an on-sensor polarizer, with each sensor line set to a different polarization angle.
Each line in a time delay integration (TDI) setup is successively struck with each of the four polarization angles (Figure 6). The four images then combine into a composite image, providing a full-resolution polarization image, versus the four-pixel interpolated image created by an area sensor like the IMX250MZR/MYR.
Conclusions
On-chip polarization sensors, now available to virtually any camera manufacturer, drive advances in software and solutions that developers and manufacturers provide for machine vision systems. An increasing number of viable polarization applications can now be expected.
No technology provides a global cure for imaging challenges, however. Polarization is another tool in the toolbox of a vision system designer or integrator.
Related stories:
Polarization in imaging: Things you did and didn’t know it could do
Experimental filter opens the door to miniature polarization cameras
About the Author
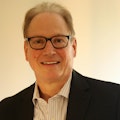
David Dechow
With more than 35 years of experience, David Dechow is the founder and owner of Machine Vision Source (Salisbury, NC, USA), a machine vision integration firm. Currently, he also is a solutions architect for Motion Automation Intelligence (Birmingham, AL).
He has been the founder and owner of two successful machine vision integration companies. He is the 2007 recipient of the AIA Automated Imaging Achievement Award honoring industry leaders for outstanding career contributions in industrial and/or scientific imaging.
Dechow is a regular speaker at conferences and seminars worldwide, and has had numerous articles on machine vision technology and integration published in trade journals and magazines. He has been a key educator in the industry and has participated in the training of hundreds of machine vision engineers as an instructor with the AIA Certified Vision Professional program.