Vision system enables autonomous forklift tasks
Researchers from the Department for Conveyor Technology, Material Flows, and Logistics at the Technical University in Munich (TUM) have developed a vision system that enables autonomous tasks involving forklift trucks in production and logistics applications.
The project, which is called "Forklift Truck Eye," involves the use of a camera on the forklifts in order to monitor and control processes in real time. Scenarios in which cameras on the forklift would be utilized include fork occupation, in which the camera identifies the forks from the image background, and if the forks can be completely detected, they are in a "free" state. The camera also monitors:
MORE ARTICLES
Automotive sensor defects detected by vision
Multi-camera vision system inspects engine rings
Industrial Automation: Robots and vision team for photonic devices assembly
- Lift height. In order to detect a shelf from which a forklift has taken a load, the lift height is determined, and in subsequent stages of development, it is possible for forklift drivers to set a lift height, which is then autonomously approached by the truck using a camera-based control loop.
- Position in space. The vision system must be able to track the position of the forklift in a warehouse. This involves either using 2D data gathered by the camera, or algorithms that detect the orientation and motion of the truck.
- Load identification. The camera is used to identify 1D and 2D codes to enable automatic tracking of material flow.
A GC2441M camera from SMARTEK Vision provided vision for the Forklift Truck Eye. The GC2441M is a 5 MPixel GigE Vision camera that features a 2/3" Sony ICX625 global shutter CCD image sensor with a 3.45 µm x 3.45 µm pixel size. The monochrome camera achieves a frame rate of 15 fps and is GenICam and GigEVision compliant. Two LEDs operated by an IPSC4-r2 4-channel lighting control system from SMARTEK were also used in the project. In addition, a software development kit from SMARTEK Vision was used to implement the software framework of the project using established image processing libraries and special detection algorithms.
By implementing the system, according to FRAMOS, the TUM researchers were able to show the benefits of integrating the vision system into the forklift truck, with the most economically profitable examples of use having been in the accurate localization of pallets. The researchers also outlined and described three scenarios in which the system could be used: Industrial users, forklift system integrators, and material handling device manufacturers.
Read more about the research project.
Share your vision-related news by contacting James Carroll, Senior Web Editor, Vision Systems Design
To receive news like this in your inbox, click here.
Join our LinkedIn group | Like us on Facebook | Follow us on Twitter | Check us out on Google +
About the Author
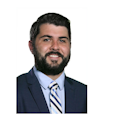
James Carroll
Former VSD Editor James Carroll joined the team 2013. Carroll covered machine vision and imaging from numerous angles, including application stories, industry news, market updates, and new products. In addition to writing and editing articles, Carroll managed the Innovators Awards program and webcasts.