Recent advancements expand the scope of 3D imaging for machine vision
Advances in 3D imaging products continue to make it easier for end users to integrate the technology into machine vision applications such as production, quality control, and metrology, further solidifying it as a mainstream technology in industrial automation. The following article looks at advances made over the last year and how these products may deploy into the real world.
Matrox Imaging (Dorval, QC, Canada; www.matrox.com/imaging) entered into the 3D hardware space with the release of its Matrox AltiZ dual-camera, single-laser 3D profile sensors (Figure 1). Targeting inspection tasks, these sensors work with Matrox Imaging or third-party machine vision software. The profilers use either red (660 nm) or blue (405) nm lasers and are built on the GigE Vision interface. Proprietary algorithms running inside the sensor automatically generate various types of 3D data—individual profiles, depth maps, or point clouds—obtained by combining or selecting the pixel data from the two integrated image sensors, which is automatically sampled for a constant horizontal resolution. The profile sensors offer IP67 rating, M12 connectors, GenICam extensions, and Power over Ethernet.
“Matrox Imaging chose to enter the 3D sensor space because our customer base had been asking for this capability, and many key customers prefer an end-to-end solution that includes software and hardware from a single vendor as much as possible,” says Pierantonio Boriero, Director of Product Management. With the Matrox AltiZ, the company offers a dual-camera, single-laser design that increases fidelity by reducing occlusions that create gaps or voids in a 3D reproduction.”
Zivid (Oslo, Norway; www.zivid.com) advanced its technology when it released the Zivid Two color 3D camera, which uses structured light to image at 2.3 MPixel resolution, at 13 exposures per 3D frame, and a minimum acquisition time of 60 ms. The camera (Figure 2) features a flexible working distance of 300 to 1500 mm, 60 µm resolution at 700 mm, 754 x 449 x 700 mm field of view, 169 x 56 x 122 mm footprint, 880 g weight, and 10 GigE interface.
Thermal and mechanical stability enhancements and floating calibration result in dimensional trueness error of less than 0.2%, while patented 3D HDR imaging and artifact reduction technology allow the camera to capture reflective and absorptive products and very small parts, according to Zivid. Additionally, the camera’s native color allows it to separate colored and similarly shaped SKUs. The Zivid Two camera targets logistics and manufacturing and supports on-arm robot deployments in applications like bin-picking and machine tending.
Related: 3D vision systems provide quality control at copper refining plant
“Zivid Two addresses key constraints found in most of today's vision systems used in pick-and-place robotics,” says Raman Sharma, VP Sales and Marketing, Americas. “Limitations like resolution, artifacts, and trueness errors restrict the optimal detection, picking, and placing of parts and objects. The new Zivid 3D camera enables deep learning, AI, and object detection algorithms to recognize more objects, plan better grasps, and place parts more reliably.”
He adds, “With the Zivid Two 3D camera, we bring together field of view, capture speed, and high-quality point cloud output in a revolutionary form-factor.”
For its part, IDS Imaging Development Systems (Obersulm, Germany; www.ids-imaging.com) released new models, the Ensenso N40/45 3D cameras (Figure 3). Made of a plastic composite material offering a lighter design, the new cameras feature IP65/67 protective housing and target robot arm or collaborative robot deployments, for example. The cameras each have two 1280 x 1024 monochrome, global shutter CMOS image sensors, screwable GPIO connectors for trigger and flash, and Power over Ethernet. Furthermore, the cameras offer an improved infrared projector that enables higher light output and optimized heat management, resulting in better data quality and increased clock rates, according to the company. The projector is optionally available with blue illumination in the visible range (465 nm) or with infrared illumination (850 nm).
The company also announced improvements for existing models in its Ensenso N 3D stereo vision cameras. Models with 850 nm infrared projection will feature new LEDs with higher light output that will result in up to 35% shorter exposure times, along with higher data quality or robustness against ambient lighting. Additionally, a new thermal design improves the projector LED duty cycle limit in all N30 and N35 Rev. 2 models by up to 10%, accelerating image capture and increasing clock rate. These updates, according to the company, may require adjustments to the camera parameters when replacing cameras in existing systems. Blue illumination (465 nm) also became available as part of Rev. 2 in January 2021.
“First of all, the new Ensenso cameras are exceptionally light, which makes them a good match for robotic applications,” says Dr. Martin Hennemann, Product Manager, 3D cameras at IDS Imaging Development Systems. “Since they are IP65/67-certified, the cameras are also sturdy and deliver high quality, filled 1.3 MPixel point clouds based on stereo vision technology. The cameras are a cost-efficient solution for 3D vision applications in production and logistics automation, i.e., object classification and dimensioning, robotic picking, packing, and palletizing, where rapid, accurate 3D volume coverage is required.”
By introducing new blue laser models to its Gocator line of 3D profile sensors (Figure 4), LMI Technologies (Burnaby, BC, Canada; www.lmi3d.com) specifically targets the 3D scanning of shiny machined-metal surfaces in applications such as electric vehicle (EV) battery inspection, rail inspection, small to medium-sized electronic and automotive parts, and general factory automation. All Gocator 2430/40/50 Blue Laser models feature a 2 MPixel camera, embedded dual core processor, and optimized optics that allow for inspection rates ranging from 320 to 5000 Hz. The 2430 and 2440 models deliver 1500 data points/profile, while the 2450 model offers 1800, depending on your application need, with measurement ranges of 80, 210, and 550 mm, respectively.
Related: 3D vision helps robots pick and disentangle hooks
Like all Gocator 3D sensors, the 2400 Blue Laser models s, feature an IP67-rated industrial housing, web-based user setup, built-in 3D visualization, drag and drop measurement tools, and numerous communication protocol options, according to the company.
“These three new line profilers add high sensitivity blue laser scanning to the 2400 series. Offering a balance of speed, high resolution data, and wide fields of view, customers can achieve precision 3D scanning and inspection of shiny surfaces with the most cost-effective sensor setup possible,” said Terry Arden, CEO, LMI Technologies.
Teledyne Imaging (Waterloo, ON, Canada; www.teledynedalsa.com) also introduced a new generation of 3D products with its Z-Trak2 series (Figure 5), which target in-line height measurements for inspection, detection, identification, and guidance in electronics, semiconductor, automotive, and factory automation market segments, according to the company. The S-2K and V-2K series feature scanning speeds of 45,000 profiles/s and 10,000 profiles/s, respectively. All Z-Trak2 models offer 2,000 points per profile, factory calibration, IP67 enclosures, and either blue or red eye safe lasers. Furthermore, both models feature 1, 2.5, or 5GigE interface; built-in reflection compensation algorithms; multi-sensor synchronizations; and high-dynamic range imaging, according to the company.
“Z-Trak3D profile sensors are unique as they contain a combination of features including high-accuracy, real-time measurements, a 5GigE interface to deliver a reach of 45K scans per second, built-in single scan HDR, and many more that enable the delivery of the most reliable 3D industrial vision solutions,” says Inder Kohli, Senior Product Manager.
In the Time of Flight (ToF) realm, LUCID Vision Labs (Richmond, BC, Canada; www.thinklucid.com) introduced its Helios2 3D ToF camera (Figure 6), which offers 2.5 times more light transmission and over 50% better 3D precision compared to the original Helios. The Helios2 features the 0.3 MPixel Sony IMX556PLR back-illuminated ToF CMOS image sensor and uses four 850 nm vertical-cavity surface-emitting lasers (VCSEL) to deliver 640 x 480 depth resolution at 30 fps up to an 8.3 m working distance. The GigE Vision 3D camera also offers on-camera processing, providing range, intensity, confidence data, and filtering options, all of which reduce the need for expensive host systems, according to LUCID.
Additional features include six operating distance modes, an industrial M12 connector for up to a 100 m cable length, sub-millimeter precision (< 1 mm measured at one meter), IP67 protection, industrial EMC immunity, an ambient light filter, multi-camera support, and the ability to combine RGB data from a color camera.
“The wide adoption of the first generation of the Helios ToF camera in applications such as 3D inspection, automated material handling, and robotics, has motivated us to further improve the performance of Time of Flight,” says Rod Barman, Founder and President at LUCID Vision Labs. “The new Helios2 ToF camera now offers even better 3D depth data precision and accuracy, a robust IP67-rated enclosure with lens protection, and a highly competitive price point.”
Specifically targeting logistics, Cognex (Natick, MA, USA; www.cognex.com) introduced the 3D-A1000 Item Detection System, a motion-capable smart camera (Figure 7) that identifies the presence or absence of objects on disparate sorters traveling at production line speeds. The system uses a patented technology called Symbolic Light, which freezes motion with a single image and gathers 3D and 2D information without the need for an encoder or field calibrations, according to the company. The factory-calibrated camera reaches a rate of 3 Hz including acquisition and on-board processing and offers Cognex software vision tools, GigE interface, IP65 protection, and can be installed and programmed in less than 15 minutes, according to the company.
“With the fusion of precise 3D and 2D images, Cognex’s advanced vision tools, and UX design, the company has taken technologies that typically require specialists to refine and packaged them into a system that newcomers to vision can setup in under 15 minutes,” says Drew Parrett, Product Marketing Manager, Cognex. “The result is a system that is easy to bring to scale and also provides more robust results against common industry challenges, such as hygiene issues degrading performance and causing maintenance headaches.”
Related: 3D-vision-guided robot automates battery production process
New to the Intel (Santa Clara, CA, USA; www.intel.com) RealSense family of depth cameras, the D455 stereo-based camera offers a longer range and increased precision that achieves twice the range of previous models, according to the company. The D455 features the 1280 x 800 OV9782 color global shutter CMOS image sensor from OmniVision Technologies (Santa Clara, CA, USA; www.ovt.com), up to 1280 x 720 depth resolution, depth and RGB frame rates of 90 fps, USB 3.1 connection, and a recommended range of 0.4 to 6 m. Additionally, the camera features a Bosch (Gerlingen, Germany; www.bosch.com) BMI055 inertial measurement unit. Powered by an Intel RealSense vision ASIC, the camera achieves less than 2% Z-error at 4 m. Intel’s latest camera targets indoor and outdoor applications including collision avoidance and object detection in robotics and drones.
“The Intel RealSense family of products now offers developers more choices,” says Joel Hagberg, Head of Product Management and Marketing for Intel RealSense Group. “The D455 expands the capabilities of the stereo camera line, addressing a wider range of applications with longer range use cases and allowing users to design solutions that best meet their needs.”
In the 3D line scan space, Chromasens (Konstanz, Germany; www.chromasens.de/en) recently introduced the 3DPIXA dual 10 µm camera based on three 15K RGB CMOS image sensors with 5.6 μm pixel size. The Camera Link, stereo line scan camera delivers 3D data and color images simultaneously and offers a 10 µm/pixel optical resolution, 150 mm field of view, a line frequency of 18.4 kHz, and is designed for use with the company’s Corona II LED line scan illumination. "What is hot for us in small 3D right now is electronics such as connector-pin, BGAs, and consumer electronics housing inspections using the Dual 15k 3DPIXA,” says Jeremy Jowers, Director of Sales and Business Development Sales Americas, Chromasens. “In big 3D, Chromasens sees geoscience and recycling applications using the 3DPIXA 200µm Dual HR (7k) and specialty OEM cameras that provide up to a 4.4 m FOV.” “Furthermore,” he adds, “Road inspection has taken life in Singapore and Japan, but Canada was first and continues to gain steam.”
Saccade Vision (Rehovot, Israel; www.saccadevision.com) offers a new 3D system for inline metrology and inspection applications. The unique technology and implementation of the Saccade-MD multi-directional 3D scanning camera (Figure 8) uses a fully programmable structured light that moves so that the part/camera does not need to move for image capture. The programmable light line can target specific areas of an image and scan at different directions to maximize the point cloud precision, according to Alex Shulman, CEO of Saccade Vision.
Additionally, the camera executes locally optimized scanning to significantly increase resolution in specific areas of the image by targeting individual features of interest.This in turn provides increased accuracy and measurement speed as compared to techniques requiring motion and full-image acquisition. The local scanning optimization and overall application configuration is done using software designed to reduce set-up time and increase ease of use, according to the company.
Related:
In March 2021, Omron Automation Americas (Hoffman Estates, IL, USA; www.automation.omron.com) will launch its FH-3D vision system. A combination of the company’s existing FH5050 vision system, the new FH-MDA 3D camera, and new 3D application software, the system targets 3D bin picking applications. The GigE 3D camera offers a 500 mm working distance measurement center, 400 x 300 x 200 mm measurement range (X,Y,Z), 0.2 mm Z direction repeatability, and a 0.5 s detection time.
The system uses the company’s Active One Shot (AOS) technology, where multiple illumination patterns project on the object and capture a 3D image of a target object in a single shot. Additionally, Omron developed a high-speed object position and orientation recognition algorithm for the 3D recognition technology.
Numerous options exist for systems integrators and end users of machine vision technology when it comes to obtaining 3D images and the list continues to grow. As it does, the machine vision community will benefit from the disparate types of 3D technologies available, speeding up and improving processes ranging from picking and placing to objection detection and dimensioning.
Companies mentioned
Bosch
Gerlingen, Germany
www.bosch.com
Chromasens
Konstanz, Germany
www.chromasens.de/en
Cognex
Natick, MA, USA
www.cognex.com
IDS Imaging Development Systems
Obersulm, Germany
www.ids-imaging.com
Intel
Santa Clara, CA, USA
www.intel.com
LMI Technologies
Burnaby, BC, Canada
www.lmi3d.com
LUCID Vision Labs
Richmond, BC, Canada
www.thinklucid.com
Matrox Imaging
Dorval, QC, Canada
www.matrox.com/imaging
OmniVision Technologies
Santa Clara, CA, USA
www.ovt.com
Omron Automation Americas
Hoffman Estates, IL, USA
www.automation.omron.com
Saccade Vision
Rehovot, Israel
www.saccadevision.com
Teledyne Imaging
Waterloo, ON, Canada
www.teledynedalsa.com
Zivid
Oslo, Norway
www.zivid.com
About the Author
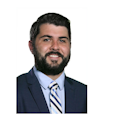
James Carroll
Former VSD Editor James Carroll joined the team 2013. Carroll covered machine vision and imaging from numerous angles, including application stories, industry news, market updates, and new products. In addition to writing and editing articles, Carroll managed the Innovators Awards program and webcasts.